Chemistry 2 - Course
#84.122
SECTIONS 202, 223, and 227
|
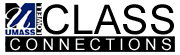 |
NEAT SCIENCE
http://nanotechwire.com/
3/2/2011 5:46:15 PM
Stronger Than Steel, Novel Metals Are Moldable as Plastic
Imagine a material that's stronger than steel, but just as
versatile as plastic, able to take on a seemingly endless variety of forms. For
decades, materials scientists have been trying to come up with just such an
ideal substance, one that could be molded into complex shapes with the same ease
and low expense as plastic but without sacrificing the strength and durability
of metal.
Now a team led by Jan Schroers, a materials scientist at
Yale University, has shown that some recently developed bulk metallic glasses (BMGs)-metal
alloys that have randomly arranged atoms as opposed to the orderly, crystalline
structure found in ordinary metals-can be blow molded like plastics into complex
shapes that can't be achieved using regular metal, yet without sacrificing the
strength or durability that metal affords. Their findings are described online
in the current issue of the journal Materials Today.
"These alloys look like ordinary metal but can be blow
molded just as cheaply and as easily as plastic," Schroers said. So far the team
has created a number of complex shapes-including seamless metallic bottles,
watch cases, miniature resonators and biomedical implants-that can be molded in
less than a minute and are twice as strong as typical steel.
The materials cost about the same as high-end steel,
Schroers said, but can be processed as cheaply as plastic. The alloys are made
up of different metals, including zirconium, nickel, titanium and copper.
The team blow molded the alloys at low temperatures and
low pressures, where the bulk metallic glass softens dramatically and flows as
easily as plastic but without crystallizing like regular metal. It's the low
temperatures and low pressures that allowed the team to shape the BMGs with
unprecedented ease, versatility and precision, Schroers said. In order to
carefully control and maintain the ideal temperature for blow molding, the team
shaped the BMGs in a vacuum or in fluid.
"The trick is to avoid friction typically present in
other forming techniques," Schroers said. "Blow molding completely eliminates
friction, allowing us to create any number of complicated shapes, down to the
nanoscale."
Schroers and his team are already using their new
processing technique to fabricate miniature resonators for
microelectromechanical systems (MEMS)-tiny mechanical devices powered by
electricity-as well as gyroscopes and other resonator applications.
In addition, by blow molding the BMGs, the team was able
to combine three separate steps in traditional metal processing (shaping,
joining and finishing) into one, allowing them to carry out previously
cumbersome, time- and energy-intensive processing in less than a minute.
"This could enable a whole new paradigm for shaping
metals," Schroers said. "The superior properties of BMGs relative to plastics
and typical metals, combined with the ease, economy and precision of blow
molding, have the potential to impact society just as much as the development of
synthetic plastics and their associated processing methods have in the last
century."
Other authors of the paper include Thomas M. Hodges and
Golden Kumar (Yale University); Hari Raman and A.J. Barnes (SuperformUSA); and
Quoc Pham and Theodore A. Waniuk (Liquidmetal Technologies).
http://nanotechwire.com/
3/2/2011 5:50:43 PM
Professor uses nanotechnology to prolong machine and engine life
Guojun Liu has discovered a way to use nanotechnology to
reduce friction in automobile engines and machines.
“The technology should be useful in a wide range of
machineries other than automobile engines,” says Dr. Liu, a professor in the
Department of Chemistry and an expert in polymer synthesis. “If implemented
industrially, this nanotechnology should help prolong machine life and improve
energy efficiency.”
Dr Liu’s team prepared miniscule polymer particles that
were only tens of nanometers in size. These particles were then dispersed in
automobile engine base oils. When tested under metal surface contact conditions
that simulated conditions found in automobile engines, these tiny particles were
discovered to have an unprecedented friction reduction capability.
Even at a low concentration, the nanoparticles performed
much better than the friction additive that is currently used by many
industries. They were able to reduce friction by 55 per cent more than the
currently achievable rate.
Dr. Liu’s discovery has earned the Society of
Tribologists and Lubrication Engineers’ Captain Alfred E. Hunt Memorial Award.
This prestigious award is given annually to the STLE member who authors the best
paper dealing with the field of lubrication or an allied field.
This is the first research that Dr. Liu has done in the
field of friction reduction and lubrication.
Dec. 20, 2010
Carbon nanotubes could be ideal optical antennae
Shivank
Garg |
An artistic
rendering of carbon nanotubes scattering light. |
By
Anne Ju
Just as walkie-talkies transmit and receive radio waves, carbon
nanotubes can transmit and receive light at the nanoscale, Cornell researchers
have discovered.
Carbon nanotubes, cylindrical rolled-up sheets of carbon atoms,
might one day make ideal optical scattering wires -- tiny, mostly invisible
antennae with the ability to control, absorb and emit certain colors of light at
the nanoscale, according to research led by Jiwoong Park, Cornell assistant
professor of chemistry and chemical biology. The study, which includes co-author
Garnet Chan, also in chemistry, is published online Dec. 19 in the journal
Nature Nanotechnology. The paper's first author is Daniel Y. Joh, a former
student in Park's lab.
The researchers used the Rayleigh scattering of light -- the same
phenomenon that creates the blue sky -- from carbon nanotubes grown in the lab.
They found that while the propagation of light scattering is mostly classical
and macroscopic, the color and intensity of the scattered radiation is
determined by intrinsic quantum properties. In other words, the nanotubes'
simple carbon-carbon bonded molecular structure determined how they scattered
light, independent of their shape, which differs from the properties of today's
metallic nanoscale optical structures.
"Even if you chop it down to a small scale, nothing will change,
because the scattering is fundamentally molecular," Park explained.
They found that the nanotubes' light transmission behaved as a
scaled-down version of radio-frequency antennae found in walkie-talkies, except
that they interact with light instead of radio waves. The principles that govern
the interactions between light and the carbon nanotube are the same as between
the radio antenna and the radio signal, they found.
To
perform their experiments, the researchers used a methodology developed in their
lab that completely eliminates the problematic background signal, by coating the
surface of a substrate with a refractive index-matching medium to make the
substrate "disappear" optically, not physically. This technique, which allowed
them to see the different light spectra produced by the nanotubes, is detailed
in another study published in Nano Letters.
The technique also allows quick, easy characterization of a large
number of nanotubes, which could lead to ways of growing more uniform batches of
nanotubes.
The paper's principal authors are former student Daniel Y. Joh;
graduate student Lihong Herman; and Jesse Kinder, a postdoctoral research
associate in Chan's lab. Park is a member of the Kavli Institute at Cornell for
Nanoscale Science. Both the Nature Nanotechnology and Nano Letters work were
supported by the Air Force Office of Scientific Research and the National
Science Foundation through the Center for Nanoscale Systems, Cornell Center for
Materials Research, Center for Molecular Interfacing and an NSF CAREER grant.
http://www.news.cornell.edu/stories/Dec10/ParkNanotubes.html
Platinum-coated nanoparticles could power fuel cell cars
Fuel cells may power the cars of the future, but it's not enough
to just make them work -- they have to be affordable. Cornell researchers have
developed a novel way to synthesize a fuel cell electrocatalytic material
without breaking the bank.
The research, published online Nov. 24 in the Journal of the
American Chemical Society, describes a simple method for making nanoparticles
that drive the electrocatalytic reactions inside room-temperature fuel cells.
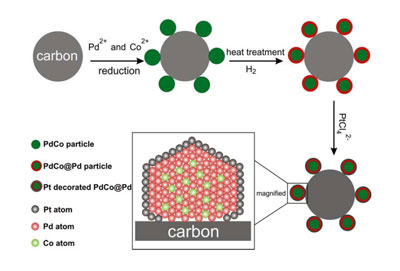
An illustration of the synthesis procedure of the core-shell
nanoparticles and subsequent deposition of platinum.
Fuel cells convert chemical energy directly into electrical
energy. They consist of an anode, which oxidizes the fuel (such as hydrogen),
and a cathode, which reduces oxygen to water. A polymer membrane separates the
electrodes. Fuel cell-powered cars in production today use pure platinum to
catalyze the oxygen reduction reaction in the cathode side. While platinum is
the most efficient catalyst available today for the oxygen reduction reaction,
its activity is limited, and it is rare and expensive.
The Cornell researchers' nanoparticles offer an alternative to
pure platinum at a fraction of the cost. They are made of a palladium and cobalt
core and coated with a one-atom-thick layer of platinum. Palladium, though not
as good a catalyst, has similar properties as platinum (it is in the same group
on the Periodic Table of Elements; it has the same crystal structure; and it is
similar in atomic size), but it costs one-third less and is 50 times more
abundant on Earth.
Researchers led by Héctor D. Abruña, the E.M. Chamot Profesor of
Chemistry and Chemical Biology, made the nanoparticles on a carbon substrate and
made the palladium-cobalt core self-assemble -- cutting down on manufacturing
costs. First author Deli Wang, a postdoctoral associate in Abruña's lab,
designed the experiments and synthesized the nanoparticles.
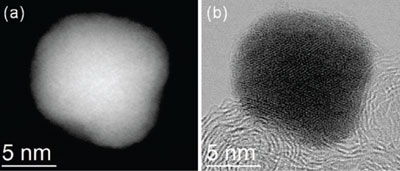
Atomic resolution images of the palladium-cobalt nanoparticle,
before platinum deposition.
David Muller, professor of applied and engineering physics and
co-director of the Kavli Institute at Cornell for Nanoscale Science, led the
efforts geared at imaging the particles down to atomic resolution to demonstrate
their chemical composition and distribution, and to prove the efficacy of the
catalytic conversions.
"The crystal structure of the substrate, composition and spatial
distribution of the nanoparticles play important roles in determining how well
the platinum performs," said Huolin Xin, a graduate student in Muller's lab.
The work was supported by the Energy Materials Center at Cornell,
a Department of Energy-supported Energy Frontiers Research Center. Researchers
also used equipment at the Cornell Center for Materials Research.
http://nanotechwire.com/news.asp?nid=11242
12/22/2010 4:08:51 PM
Ever-sharp urchin teeth may yield tools that never need honing
To survive in a tumultuous environment, sea urchins literally eat
through stone, using their teeth to carve out nooks where the spiny creatures
hide from predators and protect themselves from the crashing surf on the rocky
shores and tide pools where they live.
The rock-boring behavior is astonishing, scientists agree, but
what is truly remarkable is that, despite constant grinding and scraping on
stone, urchin teeth never, ever get dull. The secret of their ever-sharp
qualities has puzzled scientists for decades, but now a new report by scientists
from the University of Wisconsin-Madison and their colleagues has peeled back
the toothy mystery.
Writing today (Dec. 22, 2010) in the journal Advanced Functional
Materials, a team led by UW-Madison professor of physics Pupa Gilbert describes
the self-sharpening mechanism used by the California purple sea urchin to keep a
razor-sharp edge on its choppers.
The urchin's self-sharpening trick, notes Gilbert, is something
that could be mimicked by humans to make tools that never need honing.
"The sea urchin tooth is complicated in its design. It is one of
the very few structures in nature that self-sharpen," says Gilbert, explaining
that the sea urchin tooth, which is always growing, is a biomineral mosaic
composed of calcite crystals with two forms — plates and fibers — arranged
crosswise and cemented together with super-hard calcite nanocement. Between the
crystals are layers of organic materials that are not as sturdy as the calcite
crystals.
"The organic layers are the weak links in the chain," Gilbert
explains. "There are breaking points at predetermined locations built into the
teeth. It is a concept similar to perforated paper in the sense that the
material breaks at these predetermined weak spots."
The crystalline nature of sea urchin dentition is, on the
surface, different from other crystals found in nature. It lacks the obvious
facets characteristic of familiar crystals, but at the very deepest levels the
properties of crystals are evident in the orderly arrangement of the atoms that
make up the biomineral mosaic teeth of the sea urchin.
To delve into the fundamental nature of the crystals that form
sea urchin teeth, Gilbert and her colleagues used a variety of techniques from
the materials scientist's toolbox. These include microscopy methods that depend
on X-rays to illuminate how nanocrystals are arranged in teeth to make the sea
urchins capable of grinding rock. Gilbert and her colleagues used these
techniques to deduce how the crystals are organized and melded into a tough and
durable biomineral.
Knowing the secret of the ever-sharp sea urchin tooth, says
Gilbert, could one day have practical applications for human toolmakers. "Now
that we know how it works, the knowledge could be used to develop methods to
fabricate tools that could actually sharpen themselves with use," notes Gilbert.
"The mechanism used by the urchin is the key. By shaping the object
appropriately and using the same strategy the urchin employs, a tool with a
self-sharpening edge could, in theory, be created."
The new research was supported by grants from the U.S. Department
of Energy and the National Science Foundation. In addition to Gilbert,
researchers from the University of California, Berkeley; Argonne National
Laboratory; the Weizmann Institute of Science; and the Lawrence Berkeley
National Laboratory contributed to the report.
http://www.news.wisc.edu/18804
12/9/2010 11:33:02 AM
Better batteries from the bottom up
Rice University researchers have moved a step closer to creating
robust, three-dimensional microbatteries that would charge faster and hold other
advantages over conventional lithium-ion batteries. They could power new
generations of remote sensors, display screens, smart cards, flexible
electronics and biomedical devices.
The batteries employ vertical arrays of nickel-tin nanowires
perfectly encased in PMMA, a widely used polymer best known as Plexiglas. The
Rice laboratory of Pulickel Ajayan found a way to reliably coat single nanowires
with a smooth layer of a PMMA-based gel electrolyte that insulates the wires
from the counter electrode while allowing ions to pass through.
The work was reported this week in the online edition of the
journal Nano Letters.
"In a battery, you have two electrodes separated by a thick
barrier," said Ajayan, professor in mechanical engineering and materials science
and of chemistry. "The challenge is to bring everything into close proximity so
this electrochemistry becomes much more efficient."
Ajayan and his team feel they've done that
by growing forests of coated nanowires -- millions of them on a fingernail-sized
chip -- for scalable microdevices with greater surface area than conventional
thin-film batteries. "You can't simply scale the thickness of a thin-film
battery, because the lithium ion kinetics would become sluggish," Ajayan said.
"We wanted to figure out how the proposed 3-D designs of
batteries can be built from the nanoscale up," said Sanketh Gowda, a graduate
student in Ajayan's lab. "By increasing the height of the nanowires, we can
increase the amount of energy stored while keeping the lithium ion diffusion
distance constant."
The researchers, led by Gowda and postdoctoral researcher Arava
Leela Mohana Reddy, worked for more than a year to refine the process.
"To be fair, the 3-D concept has been around for a while," Reddy
said. "The breakthrough here is the ability to put a conformal coat of PMMA on a
nanowire over long distances. Even a small break in the coating would destroy
it." He said the same approach is being tested on nanowire systems with higher
capacities.
The process builds upon the lab's previous research to build
coaxial nanowire cables that was reported in Nano Letters last year. In the new
work, the researchers grew 10-micron-long nanowires via electrodeposition in the
pores of an anodized alumina template. They then widened the pores with a simple
chemical etching technique and drop-coated PMMA onto the array to give the
nanowires an even casing from top to bottom. A chemical wash removed the
template.
They have built one-centimeter square microbatteries that hold
more energy and that charge faster than planar batteries of the same electrode
length. "By going to 3-D, we're able to deliver more energy in the same
footprint," Gowda said.
They feel the PMMA coating will increase the number of times a
battery can be charged by stabilizing conditions between the nanowires and
liquid electrolyte, which tend to break down over time.
The team is also studying how cycling affects nanowires that,
like silicon electrodes, expand and contract as lithium ions come and go.
Electron microscope images of nanowires taken after many charge/discharge cycles
showed no breaks in the PMMA casing -- not even pinholes. This led the
researchers to believe the coating withstands the volume expansion in the
electrode, which could increase the batteries' lifespans.
Co-authors are Rice graduate student Xiaobo Zhan; former Rice
postdoctoral researcher Manikoth Shaijumon, now an assistant professor at the
Indian Institute of Science Education and Research, Thiruvananthapuram, India;
and former Rice research scientist Lijie Ci, now a senior research and
development manager at Samsung Cheil Industries.
The Hartley Family Foundation and Rice University funded the
research.
Read the abstract at http://pubs.acs.org/doi/abs/10.1021/nl102919m
nanotechwire.com 1/21/2011 5:09:06 PM
Butterfly wings behind anti-counterfeiting technology
Imagine a hole so small that air can’t go through it, or a
hole so small it can trap a single wavelength of light. Nanotech Security Corp.,
with the help of Simon Fraser University researchers, is using this type of nano-technology
– 1,500 times thinner than a human hair and first of its kind in the world – to
create unique anti-counterfeiting security features.
The technology is first being applied to banknotes but it
also has many more practical applications, such as authenticating legal
documents, retail merchandise, concert tickets, stock certificates, visas,
passports, and pharmaceuticals.
SFU applied sciences grad Clint Landrock started the
initial research into nanoholes under the guidance of SFU engineering science
professor Bozena Kaminska. When the pair pitched their idea to Doug Blakeway,
SFU Venture Connection’s entrepreneur in residence and also CEO and chairman of
Nanotech, he was immediately intrigued by the technology’s potential.
“I love nanotechnology but I really have not seen a
commercialization of it that can make you money in the near term,” said Blakeway.
“When this was initially presented to me by Bozena and Clint, I immediately saw
their vision and they were only after one application – creating
anti-counterfeiting features for banknotes. I felt this could be the first
commercial application of nanotechnology in the world. I kept thinking of
applications for it and how it could be used; the technologies and potential
astound me.”
Landrock and Kaminska both continue their work as part
of Nanotech’s scientific team. The company’s Nano-Optic Technology for Enhanced
Security (NOtES) product stems from an idea originating in the purest form of
nature – insects using colorful markings to identify themselves.
How this works is microscopic gratings composed of
nanostructures interact with light to produce the shimmering iridescence seen on
the Costa Rican morpho butterfly. The nanostructures act to reflect and refract
light waves to produce the morpho’s signature blue wings and absorb other
unwanted light.
The highly advanced wing structures are the result of
many millennia of evolution, and only recently have Nanotech's scientists
discovered how to reproduce these structures reliably. While others have talked
about the possibility of re-creating it, Nanotech has made this a reality.
The U.S. Treasury, which produces up to 11 billion
banknotes annually, is a potential customer for Nanotech’s product. The new U.S.
$100 bill, designed with state-of-the art security features, was supposed to be
introduced in February 2011 but it’s been delayed due to some manufacturing
issues.
Banknotes contain several security features – some that
you can plainly see and some that only machines can read – such as hologram
strips, security threads woven into the paper, watermarks, color-shifting inks,
raised type, and UV inks.
According to Blakeway, Nanotech’s product – which has
attracted the attention of treasuries internationally – is superior to holograms
and can’t be duplicated.
“Nobody has ever done this,” he said. “We have succeeded
while everybody is still trying to duplicate or imitate a butterfly’s wing
because it absorbs light and gives off the color. There’s no color pigment –
there’s nothing like a dye or anything else. It’s a hole that traps light and
releases color.
“You can’t copy or scan it in, you can’t inkjet it on
paper, you can’t do any of these things. It’s extremely sophisticated and
expensive to make the shims and dyes to produce, but very inexpensive to produce
it at the end. Anywhere you can think of where a hologram is being used today,
our technology can replace it. It’s more secure than a hologram. You can’t lift
it off – we can put it onto metal, plastic, or paper.”
SFU Venture Connections offers training and support
programs for SFU entrepreneurs. It links students, faculty and local
entrepreneurs with experienced advisors and funding opportunities.
The Secret of Bright Butterfly Wings: LED
Technology
By
Ker Than, LiveScience Staff Writer
posted: 17 November 2005 02:01 pm ET
Science was way behind nature in developing
LED light
technology, a new study finds.
The beautifully colored wings of African
swallowtail butterflies manipulate light using engineering
tricks similar to those found in digital displays. The
butterflies have black wings with
bright patches of green and blue, which they use to
communicate across long distances.
Microscopic scales covering the wings absorb ultraviolet
light and then re-emit it.
The re-emitted light interacts with
fluorescent pigments found on the butterflies’ wings to produce
the vibrant green-blue color.
Like LEDs
Researchers investigating how the scales work
found that they have many similarities to digital devices known
as light emitting diodes, also known as
LEDs, which are found in everything from computer and
television screens to traffic lights.
The first LEDs invented in the late 1960s
weren’t very bright. They produced a lot of light but most of it
tended to either become trapped inside the device or to spread
sideways and become diluted.
In the early 1990s, engineers came up with
ways to get around these problems. They outfitted LEDs with tiny
mirrors that could reflect and channel the light and made
microscopic holes in them to help the light escape.
Behind the
butterflies
While studying the wings of swallowtail
butterflies, researchers discovered that there were
a lot of similarities between the
scale coverings and LEDs.
The scales that cover the butterflies’ wings
contain tiny structures called “photonic crystals,” which act
very much like the microholes found in LEDs.
“[The scales] prevent the fluorescent light
from being trapped inside the scales and from being emitted
sideways,” said Pete Vukusic of Exeter
University, a researcher in the study.
The scales on the wing also have a
specialized mirror underneath them, which act very much like the
tiny mirrors found in LEDs.
The mirror reflects all the scattered
fluorescent light it receives upward, giving the butterflies
control over the direction in which in the light is emitted.
The
study was reported in the Nov. 18 issue of the journal
Science.
NANOTECHWIRE.COM
1/21/2011 5:06:58 PM
Nanotechnology Institute creates safe endoscopes
An interdisciplinary team of Drexel researchers have
created the first endoscope that can probe an individual cell without causing
harm - a discovery that could have wide-ranging scientific benefits, according
to project coordinator Yury Gogotsi.Gogotsi is
director of the A. J. Drexel Nanotechnology Institute as well as a materials
science and engineering professor.
The ability to inject single cells is described by
Gogotsi as "one of the pipe dreams existing for a very long time" in the field
of nanotechnology. He added that such a vision is popular in artists' renderings
for nanotechnology.
Gogotsi explained that one reason for this interest in a
single cell endoscope is because much of current cell experimentation destroys
tested cells. He said the fact that Drexel's endoscope can study parts of single
cells without affecting the cell itself "is very important for cell biology."
In addition, Gogotsi said being able to look at single
cells could greatly help researchers create new drugs.
The Drexel researchers made the endoscope by placing a
carbon nanotube, which is roughly a thousand times thinner than a human hair,
onto the tip of a glass pipette. The endoscope conducts electricity in order to
take electrochemical measurements in cells. Gogotsi said that because cells send
signals using ionic currents, "measuring these currents is very important."
The endoscope is also magnetic and fluorescent, allowing
scientists to move it around the cell and see it under a microscope.
Riju Singhal, a doctoral student in materials
engineering and a member of the project team, said the endoscope is the "most
advanced tool that exists right now for [single cell] studies."
The researchers' results were published in Nature
Nanotechnology, the top nanotechnology journal according to Gogotsi. The article
appeared on the journal's website in December and in print in January.
"Researchers in the … world are excited" about the
opportunities the cellular endoscope could create, Gogotsi said. He added that
in science many discoveries become possible due to new tools, and that "we
believe the [endoscope] will help us understand how cells function better than
we do now."
The research team has had a conference with what Gogotsi
said was a "major company" that is interested in licensing the endoscope
technology. Drexel has also filed five patent applications and two provisional
patent applications related to the project.
Gogotsi added that it could take a few years before the
cellular endoscope technology is available commercially. He said this is typical
in such situations.
The team has worked with Drexel's Office of Technology
Transfer and Commercialization, which works on protecting intellectual property
as well as marketing and licensing Drexel research.
Gogotsi said Drexel wants to "really affect [the] life
of people" through scientific and technological advances. He said he hopes the
endoscopes will eventually be produced in large quantities.
The Drexel researchers who created the endoscope come
from disciplines including electrical engineering, materials science and
engineering, biology and biochemistry and biomedical engineering.
"People with all this background were working together
as a team" to solve this issue, Gogotsi said. He credited the team's breadth of
knowledge for the creation of the endoscope.
Gogotsi said working with and learning from the members
of the interdisciplinary team was one of the most rewarding parts of the project
for him, adding that the ability to assemble a team with experts from different
fields is one example of the benefits of a research university.
The team members are a part of the A.J. Drexel
Nanotechnology Institute, which allows different disciplines to work together on
nanotechnology issues, according to Gogotsi.
He said in modern science, most discoveries are made by
teams, since most discoveries that can be made by individuals have already been
made.
Singhal said it was "a great learning experience
interacting with people from the different departments."
Singhal said the endoscope project has been his most
memorable experience at Drexel.
He added that the process was challenging and often did
not yield the desired results, but that when things worked correctly it was
"very delightful."
Singhal is currently helping with a project that is an
extension of the single-cell endoscope. The new project involves using carbon
nanotubes to remove and separate the contents of a cell. Singhal added that the
project could potentially have many industry applications for separating very
small particles, such as in crude oil.
As part of his work with the original project, Singhal
made a presentation in an engineers' conference in Vancouver, Canada. He said
other Drexel researchers have also presented on parts of the endoscope project.
Funding for the single-cell endoscope project was
provided by the W. M. Keck Foundation. The Foundation provided a grant of $1
million, according to Gogotsi, and also established the Keck Institute for
Attofluidic Nanotube-based Probes at Drexel, according to the Drexel team's
article in Nature Nanotechnology.
The Drexel team has used the Keck Foundation's funding
for the past three years, according to Gogotsi.
According to the Drexel press release on the project,
funding was also provided by a Nanoscale Interdisciplinary Research Team
National Science Foundation grant.
NANOTECHWIRE.COM 1/16/2011 5:38:48 PM
UNC researchers inch closer to unlocking potential of synthetic blood
A team of scientists has created particles that closely
mirror some of the key properties of red blood cells, potentially helping pave
the way for the development of synthetic blood.
The new discovery – outlined in a study appearing in the online Early Edition of
the Proceedings of the National Academy of Sciences during the week of Jan. 10,
2011 – also could lead to more effective treatments for life threatening medical
conditions such as cancer.
University of North Carolina at Chapel Hill researchers
used technology known as PRINT (Particle Replication in Non-wetting Templates)
to produce very soft hydrogel particles that mimic the size, shape and
flexibility of red blood cells, allowing the particles to circulate in the body
for extended periods of time.
Tests of the particles’ ability to perform functions
such as transporting oxygen or carrying therapeutic drugs have not been
conducted, and they do not remain in the cardiovascular system as long as real
red blood cells.
However, the researchers believe the findings –
especially regarding flexibility – are significant because red blood cells
naturally deform in order to pass through microscopic pores in organs and narrow
blood vessels. Over their 120-day lifespan, real cells gradually become stiffer
and eventually are filtered out of circulation when they can no longer deform
enough to pass through pores in the spleen. To date, attempts to create
effective red blood cell mimics have been limited because the particles tend to
be quickly filtered out of circulation due to their inflexibility.
Beyond moving closer to producing fully synthetic blood,
the findings could affect approaches to treating cancer. Cancer cells are softer
than healthy cells, enabling them to lodge in different places in the body,
leading to the disease’s spread. Particles loaded with cancer-fighting medicines
that can remain in circulation longer may open the door to more aggressive
treatment approaches.
“Creating particles for extended circulation in the
blood stream has been a significant challenge in the development of drug
delivery systems from the beginning,” said Joseph DeSimone, Ph.D., the study’s
co-lead investigator, Chancellor’s Eminent Professor of Chemistry in UNC’s
College of Arts and Sciences, a member of UNC’s Lineberger Comprehensive Cancer
Center and William R. Kenan Jr. Distinguished Professor of Chemical Engineering
at N.C. State University. “Although we will have to consider particle
deformability along with other parameters when we study the behavior of
particles in the human body, we believe this study represents a real game
changer for the future of nanomedicine.”
Chad Mirkin, Ph.D., George B. Rathmann Professor of
Chemistry at Northwestern University, said the ability to mimic the natural
processes of a body for medicinal purposes has been a long-standing but evasive
goal for researchers. “These findings are significant since the ability to
reproducibly synthesize micron-scale particles with tunable deformability that
can move through the body unrestricted as do red blood cells, opens the door to
a new frontier in treating disease,” said Mirkin, who also is a member of
President Obama’s Council of Advisors on Science and Technology and director of
Northwestern’s International Institute for Nanotechnology.
UNC researchers designed the hydrogel material for the
study to make particles of varying stiffness. Then, using PRINT technology — a
technique invented in DeSimone’s lab to produce nanoparticles with control over
size, shape and chemistry — they created molds, which were filled with the
hydrogel solution and processed to produce thousands of red blood cell-like
discs, each a mere 6 micrometers in diameter.
The team then tested the particles to determine their
ability to circulate in the body without being filtered out by various organs.
When tested in mice, the more flexible particles lasted 30 times longer than
stiffer ones: the least flexible particles disappeared from circulation with a
half-life of 2.88 hours, compared to 93.29 hours for the most flexible ones.
Stiffness also influenced where particles eventually ended up: more rigid
particles tended to lodge in the lungs, but the more flexible particles did not;
instead, they were removed by the spleen, the organ that typically removes old
real red blood cells.
Synthetic red blood cell mimics measuring 6
micrometers across, passing through a 3 micrometer diameter channel in a
microfludic device used to test the particles’ flexibility. The particles shown
had already squeezed through about 50 such channels without losing their shape
or elasticity. Video courtesy Timothy J. Merkel and Joseph M. DeSimone,
University of North Carolina at Chapel Hill.
The study, “Using Mechano-biological Mimicry of Red
Blood Cells to Extend Circulation Times of Hydrogel Microparticles,” was led by
Timothy Merkel, a graduate student in DeSimone’s lab, and DeSimone. The research
was made possible through a federal American Recovery and Reinvestment Act
stimulus grant provided by the National Heart, Lung and Blood Institute, part of
the National Institutes of Health (NIH). Support was also provided by the
National Science Foundation, the Carolina Center for Cancer Nanotechnology
Excellence, the NIH Pioneer Award Program and Liquidia Technologies, a privately
held nanotechnology company developing vaccines and therapeutics based on the
PRINT particle technology. DeSimone co-founded the company, which holds an
exclusive license to the PRINT technology from UNC.
Other UNC student, faculty and staff researchers who
contributed to the study are Kevin P. Herlihy and Farrell R. Kersey from the
chemistry department; Mary Napier and J. Christopher Luft from the Carolina
Center for Cancer Nanotechnology Excellence; Andrew Z. Wang from the Lineberger
Center; Adam R. Shields from the physics department; Huali Wu and William C.
Zamboni from the Institute for Pharmacogenomics and Individualized Therapy at
the Eshelman School of Pharmacy; and James E. Bear and Stephen W. Jones from the
cell and developmental biology department in the School of Medicine.
The study is an example of the type of research that
supports the Innovate@Carolina Roadmap, UNC’s plan to help Carolina become a
world leader in launching university-born ideas for the good of society. To
learn more about the roadmap, visit innovate.unc.edu.
Journal website: http://www.pnas.org
NANOTECHWIRE.COM 1/12/2011 4:24:17 PM
Argonne battery technology helps power Chevy Volt
This month, thousands of new Chevy Volt owners will begin
the real road tests of the first mass-produced plug-in hybrid electric car.
While much of the car's engineering is unique, consumers may be unaware that
some of its most extraordinary technology is inside the nearly 400-lb. battery
that powers the vehicle in electric mode.The
battery's chemistry is based in part on a revolutionary breakthrough pioneered
by scientists at the U.S. Department of Energy's Argonne National Laboratory.
The new development helps the Volt's battery—a lithium-ion design similar to
those in your cell phone or laptop—last longer, run more safely and perform
better than batteries currently on the market.
"To me this cuts right to the heart of green energy,"
said Jeff Chamberlain, who heads Argonne's battery research and development.
"This battery technology is a step towards energy independence for the U.S.; it
helps create jobs; and it can have a positive impact on the environment."
The story begins in the late 1990s, when the DOE's
Office of Basic Energy Sciences funded an intensive study of lithium-ion
batteries.
"Existing materials weren't good enough for a high-range
vehicle," explained Michael Thackeray, an Argonne Distinguished Fellow who is
one of the holders of the original patent. "The Argonne materials take a big
step forward in extending the range for an electric vehicle."
In order to improve the design, scientists had to know
how batteries worked at the atomic level.
"What we really needed to do was understand the
molecular structure of the material," said Argonne chemist Chris Johnson.
At its most basic level, a lithium battery is composed
of a negatively charged anode and a positively charged cathode. Between them is
a thin membrane that allows only tiny, positively charged lithium ions to pass
through. When a battery is fully charged, all of the lithium ions are contained
in the anode. When you unplug the battery from the charger and begin to use it,
the lithium ions flow from the anode through the membrane to react with the
cathode—creating an electrical current.
The team wanted to improve the cathode, the positively
charged material. They began by using incredibly intense X-rays from Argonne's
Advanced Photon Source synchrotron to monitor and understand reactions that
occur in lithium batteries—in real time. Next, they set out to modify and
optimize the cathode materials. Using new synthesis methods, they created
lithium- and manganese-rich materials that proved remarkably more stable than
existing designs.
Because manganese-rich cathodes are more stable than
those used in today's batteries, the new batteries are safer and less likely to
overheat. Manganese is cheap, so the battery will cost less to manufacture. The
researchers also upped the upper charging voltage limit to 4.6 volts—higher than
the usual operating voltage—and saw a tremendous jump in the battery's energy
capacity.
The Argonne battery design became, in a radical leap
forward, cheaper, safer, and longer-lasting.
"To me, that's exceptional," Chamberlain said. "New
advances often sacrifice cost or safety for performance; it's a rare
breakthrough that improves all three."
Batteries for electric and plug-in hybrid cars are much
larger—and thus far more expensive—than laptop batteries, and they make up a
large percentage of the car's price. Lowering the cost of the battery will lower
the cost of all-electric and hybrid cars, according to Khalil Amine, an Argonne
senior materials scientist, and subsequent improvements will improve battery
performance even further.
"Based on our data, the next generation of batteries
will last twice as long as current models," Amine said.
The team—especially the co-holders of the original
patent: Thackeray, Johnson, Amine, Jaekook Kim and Sun-Ho Kang—is happy to see
the technology make its way from the laboratory to the road.
"I would love to point to a car on the street and tell
my son, 'This car has our invention in it!'" Amine said.
"Seeing homegrown innovations going into a large-scale
production like the Volt—that's really exciting and good for America," Johnson
added. "It's really the ultimate goal for a researcher."
Furthermore, Chamberlain said that the new battery
technology pioneered by the lab can boost American manufacturing and create new
jobs.
"Batteries are a large, heavy component of electric and
hybrid cars, and so it's best to manufacture them near the factory where the
cars are assembled," Chamberlain explained. "This means cars assembled in U.S.
factories will also need battery factories nearby—creating more American jobs."
A total of $1.5 billion in stimulus grants went to
several companies last year—including A123 Systems, Johnson Controls and Compact
Power, an LG-Chem subsidiary—to build battery plants in the U.S. (A full list of
the grants is available online.)
Chamberlain, who worked in private industry for 13 years
before joining Argonne in 2006, says the national laboratories play a crucial
role in developing these kinds of breakthrough technologies. "The labs perform
basic research," he said. "In the U.S., businesses tend to invest in research
that will pay off in the short term; in this field of research, the national
laboratories are filling a gap by conducting the essential research that will
change the game ten to 20 years down the road."
When companies show interest in the technology, he said,
the labs collaborate with them to help adopt the method for large-scale
production.
LG Chem licensed the technology from Argonne and used
the materials to create the battery supplied for the 2011 Volt. GM has also
licensed the technology for their own tests.
"Seeing this play out is absolutely gratifying,"
Chamberlain said. "We're developing technology that I'm highly confident will
help make plug-in hybrid cars more economic. The work at Argonne ends up in the
hands of taxpayers who paid for research. This is a fulcrum, a key component to
moving away from fossil fuels."
The technology remains available for licensing.
Argonne National Laboratory seeks solutions to pressing
national problems in science and technology. The nation's first national
laboratory, Argonne conducts leading-edge basic and applied scientific research
in virtually every scientific discipline. Argonne researchers work closely with
researchers from hundreds of companies, universities, and federal, state and
municipal agencies to help them solve their specific problems, advance America
's scientific leadership and prepare the nation for a better future. With
employees from more than 60 nations, Argonne is managed by UChicago Argonne, LLC
for the U.S. Department of Energy's Office of Science.
© 2000 University of Massachusetts Lowell, Class Connections
|
Graphics & Design by: Thomas Pimental & Michelle Christman
In Association with: CLASS Connections |